BLOG
Amway Strives for Excellence Through Manufacturing
Behind every Amway product are three values that we believe make it the best in the market:
1. A commitment to the health and wellbeing of all Americans and their families.
2. A passion for consistent innovation.
3. A tireless dedication to American manufacturing.
Manufacturing high-quality products for American families is a role Amway takes seriously. Our cutting-edge technology, tried-and-true quality assurance process and devoted staff ensure that the purest, most effective products make it to your shelves.
About 70 percent of the products Amway sells in the U.S. are manufactured right here in America. Some of our employees even took the liberty of making their own T-shirts that say “The best supplier to Amway – is Amway.”
One reason that consumers know they can trust our products? Many of our popular health and wellbeing products feature plant ingredients that can be traced all the way back to where they were grown and harvested. We refer to this as “seed to supplement” development. And many of these ingredients can be found at Amway’s own Trout Lake Farm in Washington state – which produces many of the plant-based ingredients in its Nutrilite nutrition and Artistry skin care products – or from other sources. Amway provides a publicly accessible livestream of its crops at Trout Lake, emphasizing the value of transparency, and creates birth certificates for ingredients to allow the company and consumers to track their entire journey.
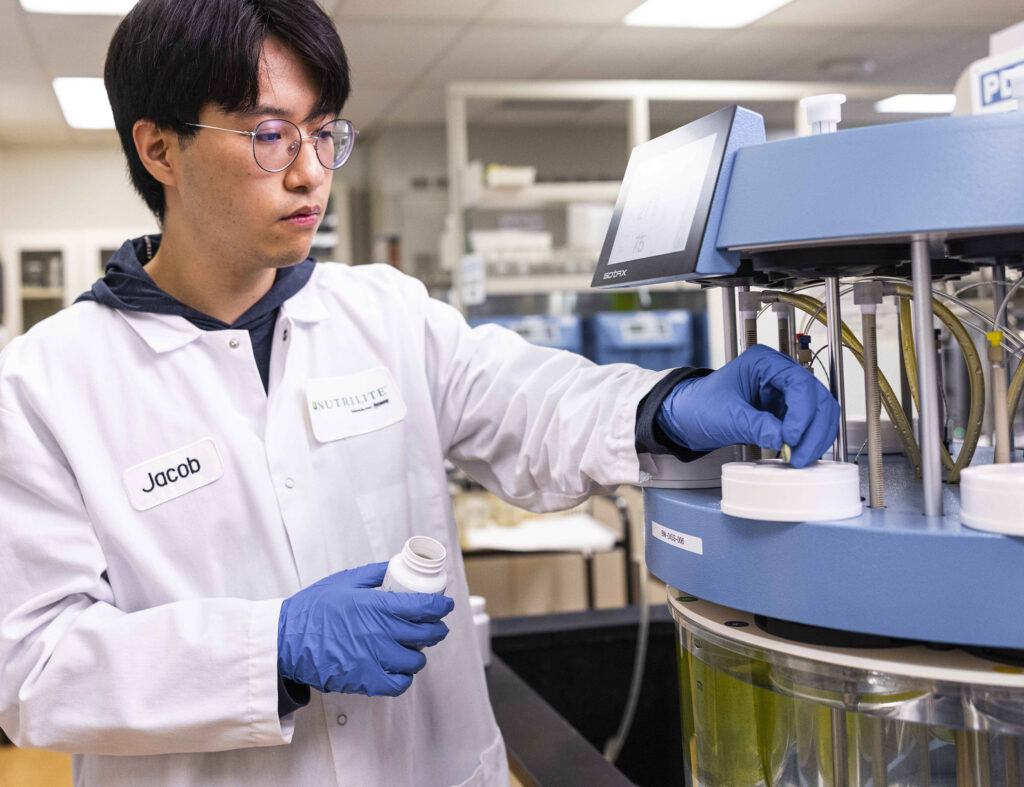
Amway’s quality assurance (QA) team ensures that all the materials are of the highest caliber. Only when ingredients pass the strict criteria established by the QA process are they sent to a manufacturing plant. Each ingredient has a scannable license that is read by a computer to determine if it is the correct weight and quantity. Then comes the actual creation of the product and, while many would think this is the final stage of manufacturing, it’s not. The assembled product must go through several packaging tests before it is approved for sale to consumers.
A second – and potentially startling – QA process occurs in Amway’s Reliability Lab or “Room of Doom” to challenge the durability of products. These tests verify if products can withstand real-world scenarios they’ll experience during the shipping process, including temperature changes, high pressure, drops and shaking. This testing assures Amway’s QA professionals that our packaged goods can be shipped across the country or around the world to its global customer base.
Amway’s Manufacturing Lead Rob Phillips, who has been at the company for 28 years, testifies to the health and wellness company’s quality assurance. “Amway is committed to making sure we send the highest quality products to IBOs, and eventually our customers.”
Every single stage of Amway’s manufacturing processes is carried out meticulously. One litmus test the company uses to test the quality of products is always asking the question “Would our staff use these products?”
The answer has been a resounding “yes!” Amway’s innovation and manufacturing staff understand the extra care taken to ensure Amway produces exceptional merchandise and many employees are avid customers of the products themselves.
Just look at Samantha “Sam” Soyka, a Packaging Department Manager who has worked at Amway for nearly 12 years. Like Rob, she’s an Amway vet and she’s experienced first-hand the consistent attention to quality that the company gives to these products.
“My family and I love Amway’s supplements. And it’s so cool because I get to oversee some of the processes that are behind the creation of these products,” said Sam. “This might be a bit weird to say, but I feel the proudest working for Amway when there is an issue of potential contamination of a product, and I see the lengths the company will go to protect its customers – they completely halt all production to get rid of the contaminant.”
When Sam was a part of the traceability team, she remembers overseeing tests that would occur every 15 minutes to ensure products were performing well. The team thoroughly cleaned the equipment after each stage of the manufacturing process to avoid quality issues. Now as a packaging manager, she’s able to witness the innovative technology Amway employs in that process, including the robots that package soft gel supplement capsules.
“We use robots to place the soft gels into cartons which they close with a tamper seal,” said Sam. “To make sure these products are still viable, the robots also use x-ray technology to look for contamination. If everything looks good, the robots complete the packaging process, and the items are ready for shipment.”
Amway goes above and beyond to provide products that Americans can trust. Whether it’s time or resources, Amway spares no expense in prioritizing innovation and manufacturing so that we can contribute to a healthier America. After all, that is Amway’s biggest priority.